Phased Array
Ultrasonic Inspection
PTC employs a superior phased array ultrasonic inspection system with 128 channels for 100% inspection of heat-treated products, featuring advanced beam steering, flaw detection, and complete traceability, operated by certified technicians and exceeding industry standards.
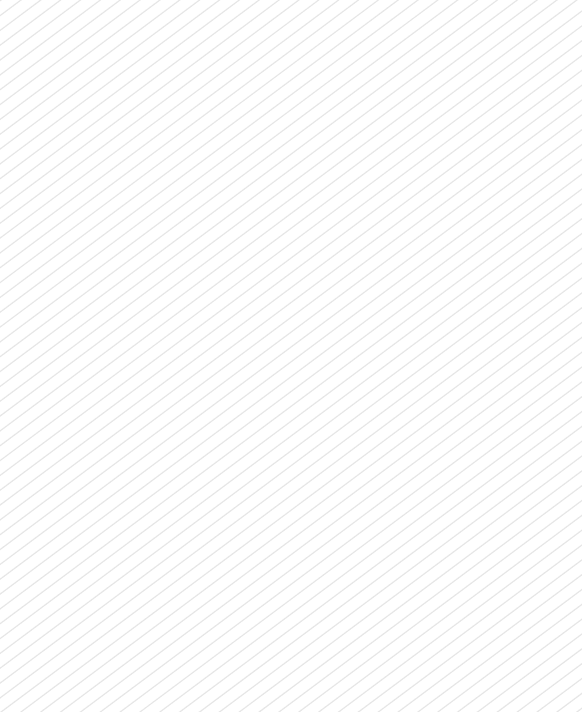
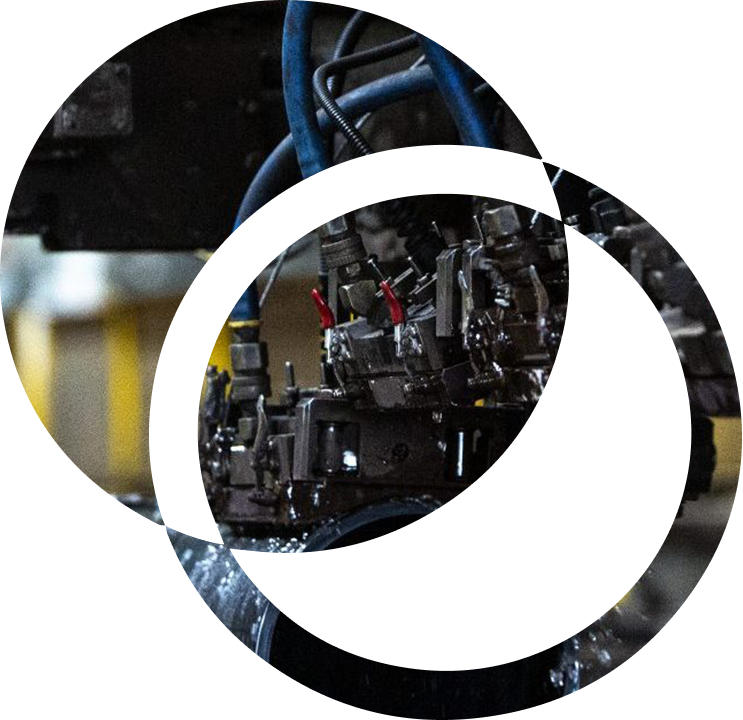
100% of PTC’s heat-treated products are inspected using a phased array ultrasonic inspection system with 128 inspection channels. It delivers an inspection that is superior over standard UT inspection with programmable beam steering and multiple flaw gates for improved discrimination and detection of flaws.
Inspection parameters for the system include 8 heads located on a dual carriage system that contain a total of 963 inspection probes for overlap coverage. Clockwise longitudinal & transverse inspection, along with counterclockwise longitudinal and transverse inspection provide the industry’s most complete inspection protocol. The system provides 100% body wall verification and end-to- end inspection capability which eliminates the need for Special End Area (SEA) inspection.
Each pipe is marked with a stencil that identifies each joint uniquely to ensure we have complete traceability and identification.
The equipment is operated by our UT technicians who are trained and certified to meet ASNT requirements for Phased Array UT operators as outlined by American Society for Non-Destructive Testing.
Each tube has a physical verification of the PTC RTIS stencil prior to shipment, and each tube has a physical check verifying the heat, grade and gauge prior to shipment.
Complete inspection reports are available to provide all pertinent information regarding lot number, inspections performed, size, weight, grade, threads, number of joints, and total footage of prime material.
Current set points on all materials for hydrostatic testing is 90% SMYS (Specific Minimum Yield Strength) vs 80% as specified by API.
Calibration and Inspection Levels
*t=Nominal Pipe Thickness
Related Products
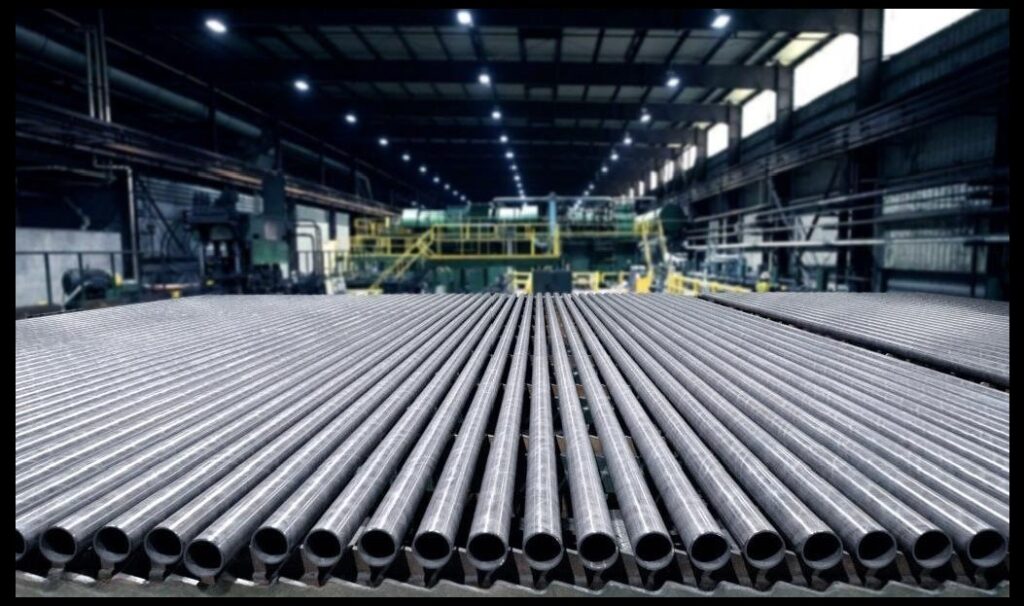
Electrical Resistance Welded (ERW Casing) for OCTG
PTC leads in ERW tubing for OCTG, crafting high-grade pipes in Liberty, Texas with advanced NDT, uniform thickness, and robust performance.
Learn more
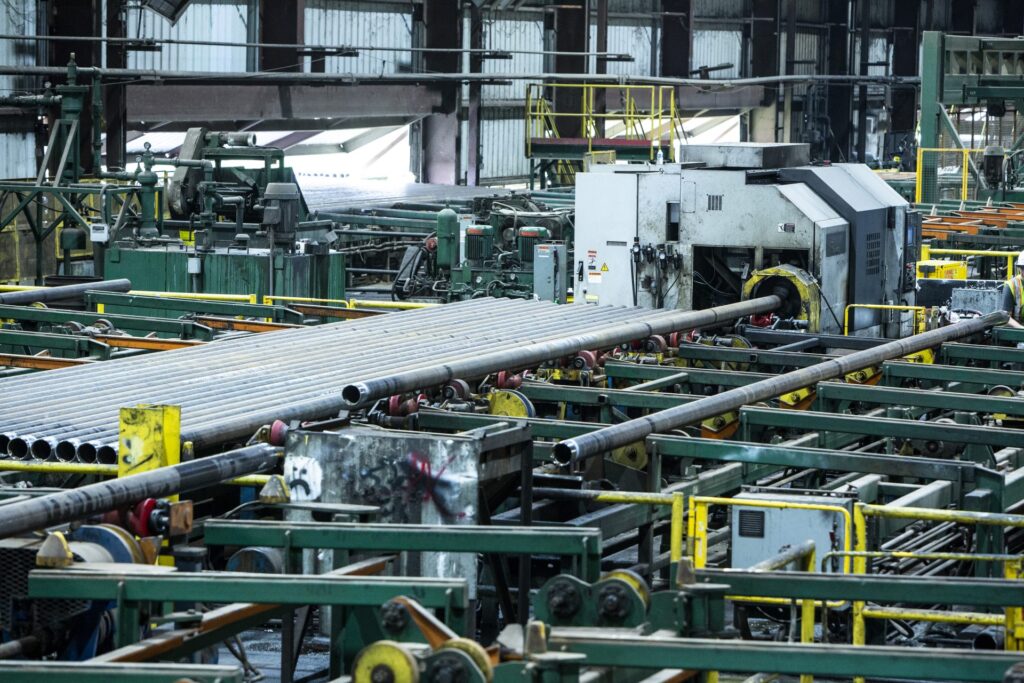
API and Semi-Premium Threading
PTC leads in Semi-Premium & API Certified Threads for OCTG. Superior threading with PMC & Mori Seiki machines, meeting API 5CT, 5L, and 5B standards.
Learn more
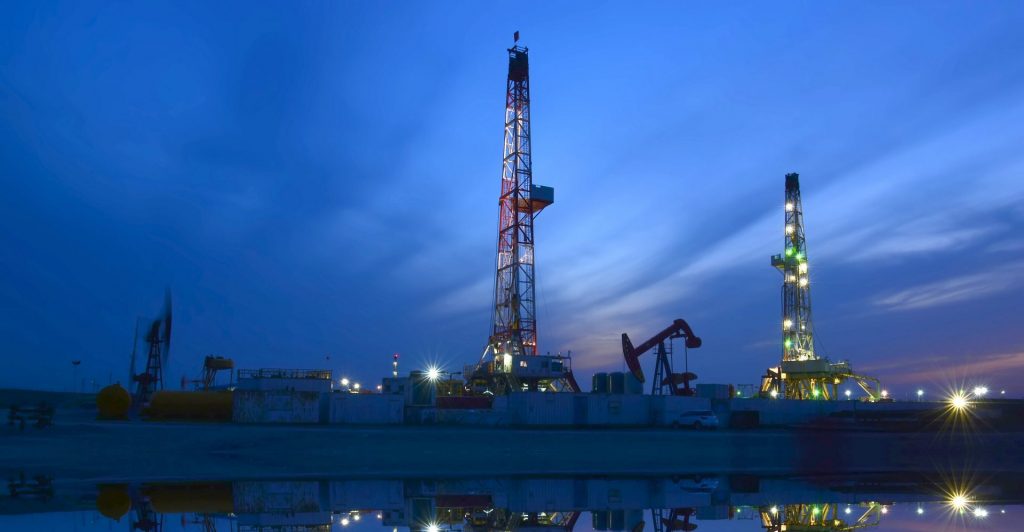