Quality Assurance
PTC's Quality Assurance program exceeds API specifications through a comprehensive approach that includes advanced quality systems, meticulous metallurgical oversight, rigorous quality control inspections, state-of-the-art phased array ultrasonic inspection, and stringent collapse testing to ensure product reliability and performance.
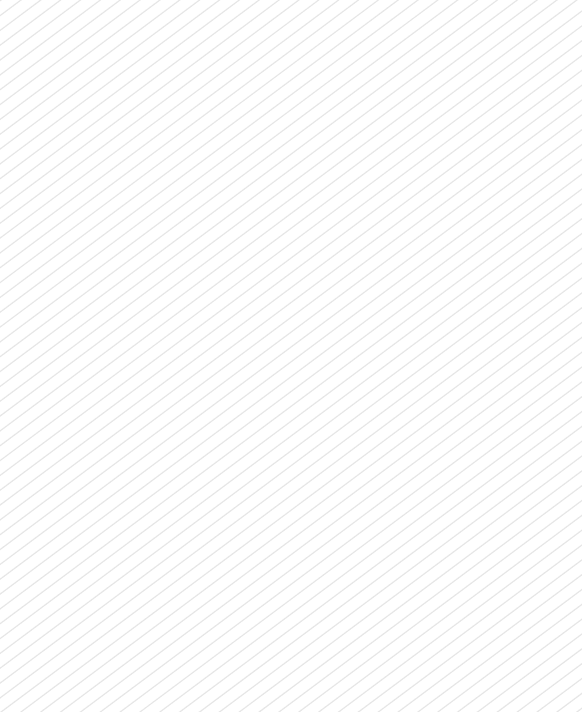
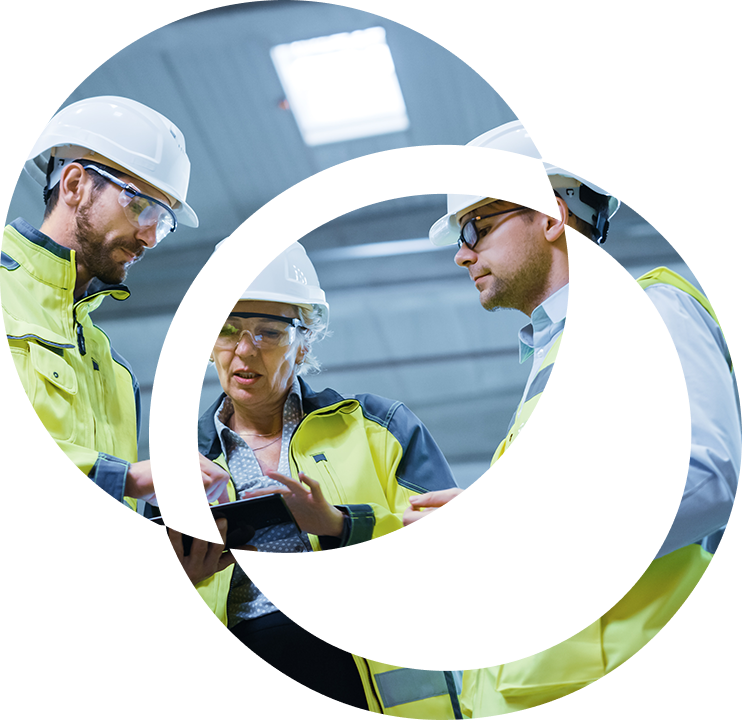
PTC’s Quality Assurance program for manufactured products was developed to meet and exceed the American Petroleum Institute (API) specifications for the manufacturing of casings.
In addition, API sets forth requirements for a quality system which must conform to all requirements as set forth by the API Q1 Program. Many of PTC’s tolerances are set at one-half of the API requirements.
PTC has developed a Quality Assurance program focusing on five major components:
- Quality Systems: Our quality systems establish compliance with API Q1 requirements for control of documentation, verification, vendor approvals, audits, and implication of product realization from order entry to order completion.
- Metallurgical and Laboratory Oversight: These include steel sourcing, incoming product verification checks, process control checks, and final product validation. This is accomplished by chemical testing, mechanical testing, Charpy impact testing, and microscopic evaluations of weld and steel quality.
Metallurgy also establishes heat treating and processing parameters for PTC heat-treat lines and verifies that the proper parameters are met by validation of the process parameters, mechanical testing, and metallurgical evaluation of microstructures.
PTC’s laboratory personnel also secure tube samples and perform collapse testing evaluations of various pipe grades to assure that the pipe can meet or exceed API or customer requirements for resistance to external pressures. We own and utilize the most advanced state-of-the-art collapse testing equipment in the world. - Quality Control Inspection: Inspection of the products in process includes ultrasonic inspection of the welding process immediately after forming and joining the pipe edges.
Destructive testing of pipe rings is performed to verify the pipe is capable of deformation by crushing to a minimum required value as set forth by API standards; after meeting API standards, the samples are crushed completely to further verify performance parameters.
Quality Control personnel perform full body electromagnetic inspection of pipe immediately following hydrotest to a specified pressure. A final visual inspection of the pipe is made immediately following the electromagnetic inspection to assure proper dimensional values and straightness of the products.
Quality control inspections are also performed on the threaded ends of the pipe to assure that they meet all API and customer requirements for lead, taper, standoff, thread height, ovality, and thread length.
Thread inspection includes visual examination in conjunction with comparator evaluation of thread elements and thread profiles. - Phased Array Ultrasonic Inspection: PTC conducts inspections of 100% of our heat-treated products utilizing our RTIS inspection system. This state-of-the art unit enables PTC to provide the most complete, accurate, and stringent inspection in the industry.
Phased array technology gives us the ability to fully inspect the pipe body and the weld-line for each joint. This unit is the most advanced inspection unit known to exist in any mill environment.
While some mills recently began adopting this technology, we’re unaware of any mill adhering to the strict inspection criteria and standards enforced by PTC in the utilization of this equipment. - Collapse Testing: PTC has invested in the most advanced collapse testing equipment in the industry that is custom manufactured for PTC. PTC uses 8 times diameter samples to provide a more representative and stringent collapse test for all collapse tested products.
Related Products
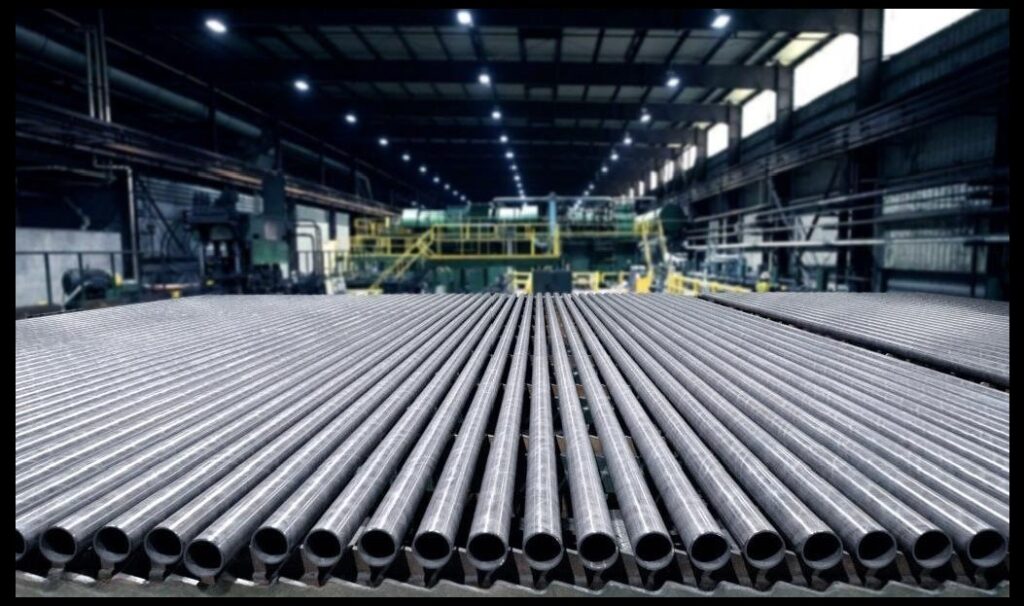
Electrical Resistance Welded (ERW Casings) for OCTG
PTC leads in ERW pipe for OCTG, crafting high-grade pipes in Liberty, Texas with advanced NDT, uniform thickness, and robust performance.
Learn more
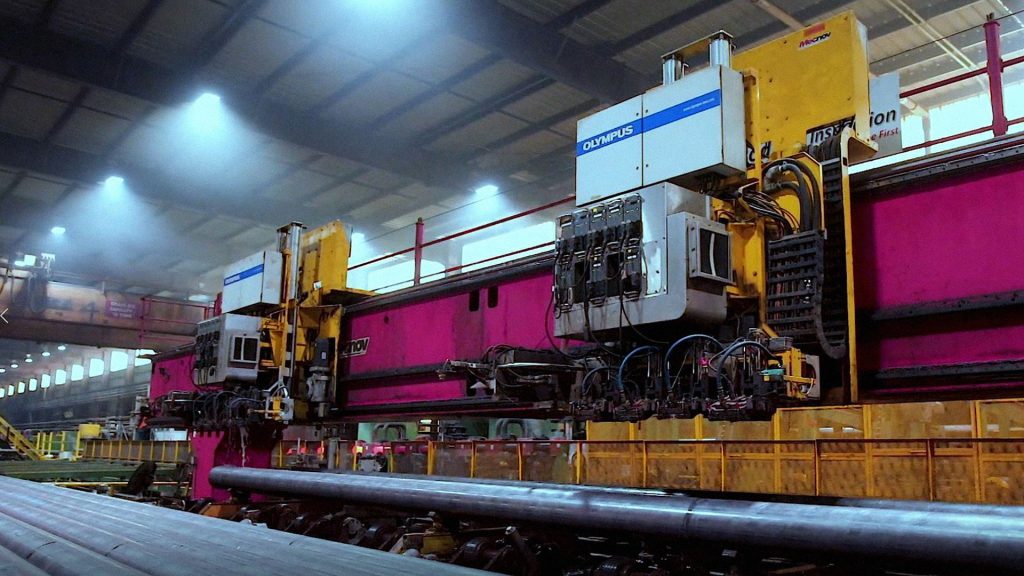
Phased Array Ultrasonic Inspection
PTC, a leader in ERW pipe production for downhole casing, offers up to 9.625” OD in various grades and threads, featuring advanced testing and uniform thickness.
Learn more
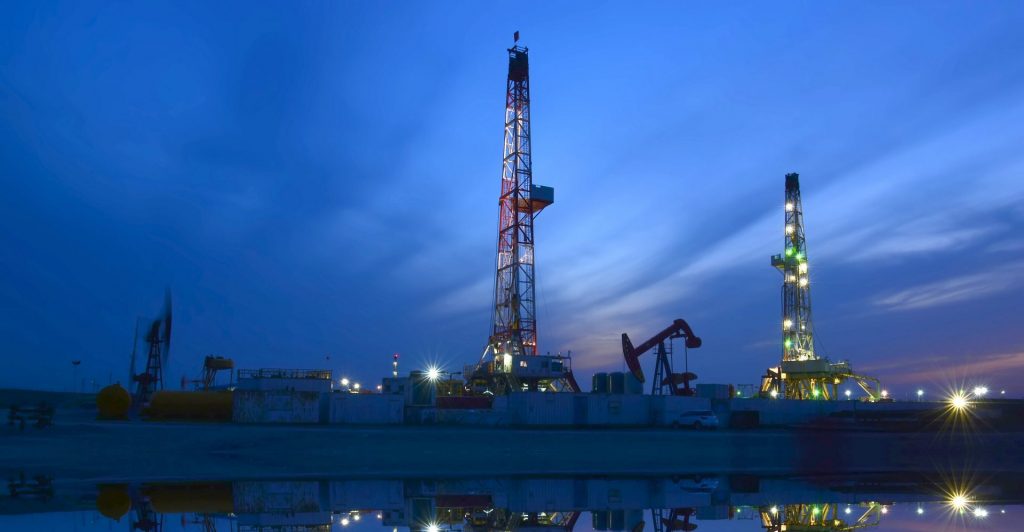